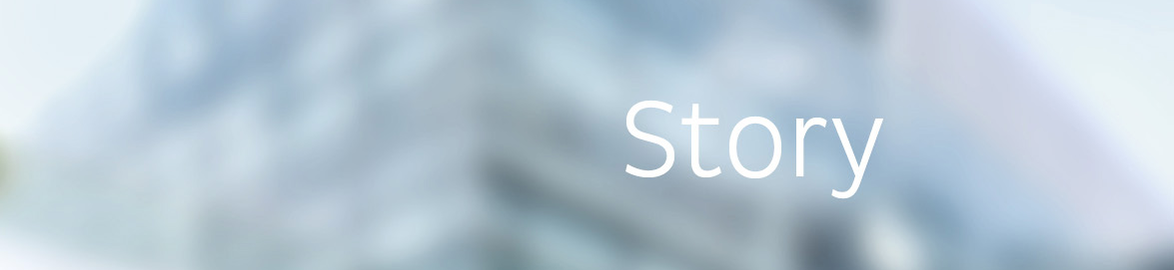
Reduction of hazardous emissions by more than a billion tons
22.03.2017 — Today, there are over a billion vehicles on the roads and this is likely to increase to 1.2 billion by 2018. Exhaust catalytic converters manufactured by BASF Catalysts Germany GmbH in Nienburg, Lower Saxony, ensure that the majority of hazardous substances are removed from exhaust emissions. Dussmann Service is responsible for security at the production plant.
It’s not a pretty sight nor is the description attractive: “slurry”. But it is extremely valuable slurry; it contains three precious metals rhodium, palladium and platinum. These are used for the washcoat on ceramic or metal molds used to make the vehicle catalysts which convert hazardous emissions. There are a few grams of precious metals in every ready-for-use catalyst which vary from bucket to thimble sized depending on whether they serve a heavy vehicle or a scooter.
The catalysts division at BASF is a global market leader of catalyst technology. Almost all of the top automobile brands equip their vehicles with a catalyst manufactured by the BASF subsidiary to convert carbon monoxide, nitrogen oxide and volatile hydrocarbons into water, nitrogen and carbon dioxide. Over 95 percent of emissions are eliminated in this way (See box on page 17). The headquarters of the European Catalyst Division which includes research and sales is located in Hanover. The production plant is in Nienburg/Weser.
A solution for each vehicle
Each motor requires a specific catalyst depending on its emissions; this is the challenge. Even for individual models, customers have the choice between numerous different motors and that means different exhaust content and different catalytic converters. The specialists at BASF are familiar with the process. “It’s especially dramatic when a car manufacturer changes the order at short notice” reveals Dr. Martin Kraum, plant manager at the BASF emissions catalytic converter plant in Nienburg. “Sometimes, we have only 14 days to adjust machines, order monoliths and prepare the washcoat.”
Difficult to imagine today: emissions 40 years ago
Huge progress has been made; today, 100 cars generate about the same amount of hazardous emissions as a single vehicle did in 1974 before the introduction of catalysts. And the question is still: how can we reduce emissions even further using even fewer materials? There are two things that experts can influence: the monolith and the washcoat. “The finer the canal that the exhaust passes through, the more hazardous particles can be converted” explains plant manager Kraum. “But if it’s too narrow, it’s like squeezing the neck of a runner. Respiration is seriously compromised.” The developers’ greatest opponent is the heat that is generated in and around the catalyzer during operation. The metals used must withstand temperatures of over 1,000 degrees Celsius and legislation requires that a catalyst has a life of at least 160,000 kilometers. In a laboratory at BASF Catalysts Germany GmbH in Hanover, researchers examine products and technologies at engine test benches. Catalysts are tested under all sorts of conditions and subjected to various stress tests. It was in this spirit of research that the new EMPRO FWCTM fourway catalytic converter was developed. The performance of a modern three-way catalytic converter is combined with a particle filter. The catalyst makes it possible to comply with the new Euro-6c limits without negatively influencing performance and motor wear and tear.
Successes like this are the results of a strong group of companies to which the catalyst manufacturer belongs. In 2006, BASF—the largest chemical company in the world—acquired the US-American Engelhard Corporation, which invented the first commercial three-way catalytic converter. The workforce joined like-minded specialists at the BASF Group who demonstrate the same enthusiasm and expertise for paints, plastics, carrosserie and batteries in the automobile sector.
Security is important
What with the research and development department, precious metals, and the safety challenges presented by chemical production, security plays a major role at BASF Catalysts Germany. In July 2014, the Dussmann Service team began security operations on the company’s site in Nienburg. They ensure that only authorized personnel enter the site, that safety risks at the production plant are kept to a minimum and that no one and nothing leaves the site unnoted. The security guards cover operations around the clock, 365 days a year.
In January 2016, cutting edge security technology was installed. The reconstruction of the entrance area took over a year and was the first project supervised by the new head of security, Ulrich W. Müller. “Every person and every vehicle is checked and digitally registered” explains Müller. Our state-of-the-art luggage scanner would make many airports envious.”
All vehicles entering and leaving the site must pass a check point with two consecutive gates. Electronic locks ensure that only one gate is open at any time. Three receptionists monitor the road safety of the vehicle, documentation and load. “We have found the most amazing things in vehicles” grins Dussmann site manager David Klijnstra.
“A large knife under the driving seat, for example. Worn tires or out-of-date MOTs compromise safety and such vehicles are not allowed onto the site”. It’s a balancing act between thoroughness and keeping traffic moving—a mix of heavy vehicles, cars and fork-lift trucks.
The Dussmann team is the first contact for visitors to BASF Catalysts Germany who can expect a friendly welcome, both personally at reception and by phone. Distribution of external and internal mail is also one of team’s duties. Video cameras in the production plant and all over the grounds are connected to the security center around the clock.
The security head at Niendorf, Müller is happy with the Dussmann team. “We agree on the approach to the things that need doing and we work together on ensuring optimum security on the site” he says of the cooperation. Coordination is uncomplicated and paths of communication short. During the reconstruction, Müller ensured that his office was located directly at visitor reception.
The Dussmann team does a good job and this was recently officially recognized during an audit carried out by experts from company headquarters in Ludwigshafen; the security procedures in Nienburg attracted high praise.
Dussmann Newsroom
News
News, stories, downloads and images - everything about Dussmann and the business units Facility Management, Food Services and Technical Solutions can be found in the Newsroom. Take a look and get to know us better!