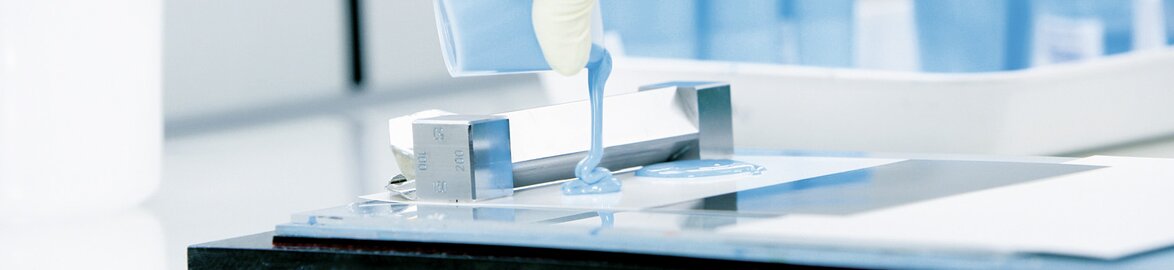
Of Free-Thinkers and Packaging Artists
22.07.2015 — The producer of specialty chemicals, Altana is one of the most innovative and viable companies in the industry. This is due, not only to its generous research and development budget but also to the very special corporate culture that the company has succeeded in cultivating. Employees take on responsibility and know that unconventional ideas are taken seriously. Dussmann personnel, who provide catering services at the staff restaurants at company headquarters in Wesel am Niederrhein, are aware of the very special atmosphere among the workforce.
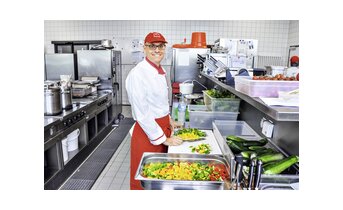
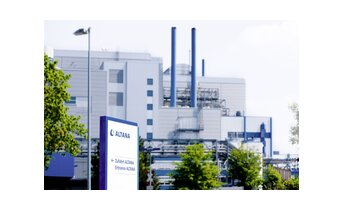

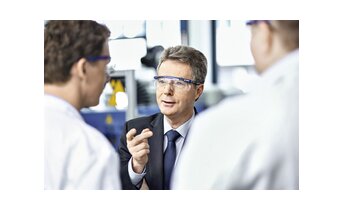
Saddle of lamb with roast vegetables was on the menu at the Altana AG staff restaurant in Wesel am Niederrhein. Restaurant guests have come to expect a varied, appetizing selection and so there ought not to have been anything unusual about it. But there were smiles all round when the cook of the day introduced himself; CFO, Martin Babilas had exchanged his desk for the hot stove and helped serve the meal at the service counter at lunchtime. Dussmann site manager, Oliver Nöltge gave his aide a good report: “It is a challenge to cook for 300 guests, even for an experienced hobby cook”. Close proximity to the workforce is a matter of course at Altana even though the company is no longer a modest family business; over 6,000 people work at 49 production plants and 50 application and research laboratories across the world. They develop and produce high-grade, innovative specialty chemical products. All over the world, paint manufacturers, synthetics processing and clients in the printing, cosmetic and electrical industries rely on products from the four Altana company divisions. One example is an additive produced by BYK Additives & Instruments: the addition of even a small amount makes paints scratch-resistant, help them to dry faster and enhances the final gloss. Eckart Effect Pigments heighten the glamor of nail varnish, lip sticks and packaging. The lid on the pickled gherkin jar is leak-free thanks to the seal provided by Actega Coatings & Sealants. And lastly, insulation materials produced by Elantas Electrical Insulation make electric motors, TV sets, wind turbines and computers progressively smaller and more efficient. A key element of these successes is the special atmosphere at Altana. The CFO and chef who, like the other board members, eats in the same staff restaurant as the rest of the workforce, offers an explanation: “We are the market leader for all types of specialty chemicals” explains Martin Babilas. “This is because of ongoing innovation both in terms of products and processes. And innovation is best generated through dialogue between colleagues across hierarchies and departments.” There is an ambitious budget for research and development; Altana invested 6 percent of annual turnover in R+D, almost twice the average amount in the industry and it was not reduced during the crisis years 2008/2009. One in six of the chemical company’s employees works in the R+D department.
Scratch-free
One of them is Marcel Altenburg. The young chemist who is only 24 years old started his apprenticeship eight years ago in the division Actega in Lehrte, Lower Saxony. Today, he works together with four colleagues, all of whom are aged around 30, in the research and development section Flexible Packaging / Labels on developing perfect UV and water-based paints for packaging and labels. What are the characteristics of good synthetic packaging? For foods, it must be visually attractive but also environmentally compatible, odorless and tasteless. On their way from production via the wholesaler to the retailer and finally the consumer, the packages are put to the test. They are filled with hot or cold foods, stacked, packed, heated, cooled and rinsed. This applies especially in the case of so-called in-mold labeling. Whether it carries ice cream, margarine or paint, the labeling is integrated during the casting process. This looks goods, reduces production time and costs and is environmentally compatible because it is easy to recycle. However, the coating suffers from light scratching. This compromises the appearance and may cause the customer to reach for an alternative, more attractive product. This was the challenge presented to the F+E team in Lehrte - to produce a hard-wearing coating for in-mold labeling with the required effect. The project was launched: Marcel Altenburg took on responsibility for the development of such a coating in the laboratory together with a team made up of developers, technicians, and product managers that was assembled specifically for the project. This is how employees become entrepreneurs within the company. “We encourage free-thinkers and rebels in a positive way. In many companies this sort of attitude can cause difficulties” explains Dr. Georg F. L. Wießmeier, Chief Technology Officer (CTO) with responsibility for innovation. “Career entrants can often provide important leads and ideas because they in a better position to question established processes”. This was the background to the development of extremely scratch and abrasion-resistant, water-based coatings at Actega in Lehrte. They dry in seconds, tolerate extreme temperature differences during the production process and, importantly, comply with food legislation. The new product line is already making money in the same year that it was introduced; this is impressive, even for Altenburg’s employer and the team in Lehrte was awarded the Altana Innovation Award in 2013. The award honors the company’s best innovations, preferably those involving a number of departments.
The role of the manager
The new coatings are one of numerous product innovations by Altana. Between 15 and 25 percent of turnover in the four divisions is generated by products which are five years old or younger. The company’s success is dependent on them and managers at other German manufacturers agree on the importance of innovation. Last year, Altana contracted the Forsa institute to carry out a survey of 250 decision makers for the second time. For the “industrial innovation index 2015” decision makers rated the significance of innovation on a scale of 1 to 10 resulting in an average of 8.7. Over a third of the participants plan a larger budget for innovation in 2015. Apart from financial investment, the managers were critical of their own operations. 32 percent rate the ability to innovate as very important but only six percent classify their own company as very innovative and, according to the managers who participated, only every tenth industrial enterprise provides sufficient freedom and acceptance for unconventional thinking and action. Even their own role as manager is perceived critically; only 16 percent believe that they contribute significantly to a culture of innovation. More about the industrial innovation index 2015 at www.altana.de/presse-news/presse-news.html As a consequence, aspiring managers at Altana need to offer more than excellent professional skills and knowledge. Personal characteristics such as curiosity, openness and the willingness to question traditional structures and processes are as least as important. Managers often participate in training and learn to motivate their teams, to take on responsibility and to find construction solutions together. Young talent is expressly deployed in projects which involve a number of departments; this encourages free-thinking and creates effective contact networks. CTO Wießmeier is convinced that “only if we work together closely with the client can we anticipate his wishes and develop successful solutions”.
Understanding what the client wants
To understand day-to-day operations at Altana, we visit Martin Fischer. The chemical engineer, who also has experience of plant construction, works in the division BYK Additives & Instruments, in Wesel. As the applications manager for PVC& leather, Fischer is an important contact for PVC processing companies. When manufacturing floors, carpets, wallpaper or synthetic leather, a high speed coating process produces a layer of PVC plastisol only millimeters thick. Productions plants are often over 500 meters long and up to 30 meters of floor covering or 100 meters of wallpaper are produced each minute. Because the viscose plastisol flows unevenly, manufacturers add a “Rheology additive” from BYK . However, it is an intricate task to determine the proportion of additive to plastisol; the measurement procedure used in the laboratory cannot be deployed under production conditions. Anticipating client requests? Martin Fischer can tell you about it: BYK decided to replicate the client’s production conditions to be able to develop reliable recommendations using a miniature coating plant. The investment plan prepared by Fischer and his team persuaded executive management and after only six months for development, BYK started operations on its own eight meter long production plant in 2013. The plant has everything that its big sister has in miniature form and enables the team to determine the optimum dose for various flow speeds and coating widths. Clients are impressed and enthusiastic about the service. PVC manufacturers and processors across the world now have their individual applications checked by BYK in preparation for live production.
Dussmann Newsroom
News
News, stories, downloads and images - everything about Dussmann and the business units Facility Management, Food Services and Technical Solutions can be found in the Newsroom. Take a look and get to know us better!